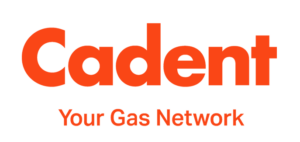
Advancing Asset Management Maturity at Cadent Gas
Explore the concept of Asset Management maturity and its impact on organisational success in this insightful case study post.
In this case, the organization was seeking to reduce costs whilst maintaining performance and managing risks by optimizing its maintenance strategy. Intervals for intrusive planned maintenance had been extended, with increased use being made of condition monitoring techniques to target activities where they are needed. There was a long-established practice of annual trip test operation of circuit breakers but the organization wanted to ascertain whether this was a worthwhile exercise and to determine the optimum frequency that such testing should be carried out.
Electrical distribution utilities use medium voltage networks for the distribution of electricity from primary substations to local distribution substations close to the point of load. In many parts of the world, distribution utilities use 10-13kV levels as the final step down before final low voltage delivery connections. At each of these voltage step-downs and network connecting points, circuit breakers are used for protection and switching purposes. These breakers can use a variety of technologies, such as oil or sulphur hexafluoride gas as an arcing suppression medium. There are many circuit breakers in service in a typical network; they are highly reliable and, in a protection/isolation role, normally remain passive until called upon to operate under fault conditions. It is clearly essential that they operate correctly and rapidly when called upon to operate to disconnect a fault. failure to do so can result in transformer overloading (potential explosion) and other hazards to people and network equipment.
We were called in to support a multi-disciplined team study of the optimal testing strategy using the SALVO Process. This provides a structured navigation and evaluation discipline to ensure all factors, stakeholder interests, uncertainties, and scenarios were explored, quantified, and evaluated on a consistent and auditable basis. This process was supported by real-time cost/risk modeling and ‘what if?’ calculations using the DST Inspection Evaluator™ tool.
This case involved a small team comprising process safety personnel. It needed just 2 hours to build the basic scenario, using the SALVO storyboard for inspection decision-making, and DST Inspection Evaluator™ to model the risks and costs, and operational options available, and identify the optimal strategy. The team also developed a number of alternative scenarios and explored their impact on the optimum strategy. The study, including analysis of sensitivity to all sources of data uncertainty, revealed that the optimal strategy was to carry out functional testing every 48 months. The major factor in determining the optimum interval proved to be the direct cost of the labor for carrying out the test. The marginal increase in risk as a result of extending the test interval was carefully explored, considered acceptable, and did not impact safety. Finally, a formal decision-recording stage ensured the capture of the optimal strategy, the implementation actions, and the audit trail so that the proposed change is fully documented and future revisions can easily understand why the strategy was set to 48-monthly.
To perform the complex reliability, risk and financial ’what if?’ calculations, this study used decision-support software called DST Inspection Evaluator™. This tool was developed as part of the international SALVO project to support the analysis of asset inspection and condition monitoring decisions. Like other modules in the DST Asset Strategy Evaluator™ suite, the tool provides:
The cost/risk calculations revealed that the optimal interval for testing was at 48 months, rather than the existing 12 monthly cycles. This extension of testing interval yields a c.75% reduction of overall business impact (costs and risks). For the population of 4,000 such circuit breakers, this represents a potential saving of £156,000 per year. These values take account of the risks of switchgear functional failure due to ‘hidden’ failure modes, the cumulative deterioration risks between tests, switching, and other costs of the trip-test itself. And it also incorporates any beneficial effects (e.g. grease redistribution reduces ‘stiction’) or failure risks introduced by the testing activity.
The Woodhouse Partnership would be delighted to show you how the SALVO process and Decision Support Tools™ can be implemented to benefit your business, contact us now for a free initial consultation. We look forward to hearing from you.
Explore the concept of Asset Management maturity and its impact on organisational success in this insightful case study post.
Grupo Energia Bogota (GEB) is a public utility corporation with more than 125 years of history.
Mutual Energy has been recognised for effective asset management of critical infrastructure by achieving ISO 55001 certification.
Cookie | Duration | Description |
---|---|---|
cookielawinfo-checkbox-advertisement | 1 year | Set by the GDPR Cookie Consent plugin, this cookie is used to record the user consent for the cookies in the "Advertisement" category . |
cookielawinfo-checkbox-analytics | 11 months | This cookie is set by GDPR Cookie Consent plugin. The cookie is used to store the user consent for the cookies in the category "Analytics". |
cookielawinfo-checkbox-functional | 11 months | The cookie is set by GDPR cookie consent to record the user consent for the cookies in the category "Functional". |
cookielawinfo-checkbox-necessary | 11 months | This cookie is set by GDPR Cookie Consent plugin. The cookies is used to store the user consent for the cookies in the category "Necessary". |
cookielawinfo-checkbox-others | 11 months | This cookie is set by GDPR Cookie Consent plugin. The cookie is used to store the user consent for the cookies in the category "Other. |
cookielawinfo-checkbox-performance | 11 months | This cookie is set by GDPR Cookie Consent plugin. The cookie is used to store the user consent for the cookies in the category "Performance". |
elementor | never | This cookie is used by the website's WordPress theme. It allows the website owner to implement or change the website's content in real-time. |
viewed_cookie_policy | 11 months | The cookie is set by the GDPR Cookie Consent plugin and is used to store whether or not user has consented to the use of cookies. It does not store any personal data. |
Cookie | Duration | Description |
---|---|---|
_icl_visitor_lang_js | 1 day | This cookie is stored by WPML WordPress plugin. The purpose of the cookie is to store the redirected language. |
aka_debug | session | Vimeo sets this cookie which is essential for the website to play video functionality. |
wpml_browser_redirect_test | session | This cookie is set by WPML WordPress plugin and is used to test if cookies are enabled on the browser. |
Cookie | Duration | Description |
---|---|---|
_ga | 2 years | The _ga cookie, installed by Google Analytics, calculates visitor, session and campaign data and also keeps track of site usage for the site's analytics report. The cookie stores information anonymously and assigns a randomly generated number to recognize unique visitors. |
_gat_gtag_UA_20267140_1 | 1 minute | Set by Google to distinguish users. |
_gid | 1 day | Installed by Google Analytics, _gid cookie stores information on how visitors use a website, while also creating an analytics report of the website's performance. Some of the data that are collected include the number of visitors, their source, and the pages they visit anonymously. |
vuid | 2 years | Vimeo installs this cookie to collect tracking information by setting a unique ID to embed videos to the website. |
Cookie | Duration | Description |
---|---|---|
wp-wpml_current_language | 1 day | No description available. |
Introducing DST v4 – our most advanced upgrade yet.
Elevate your decision-making capabilities and experience.
Discover the future of decision support with DST v4.
Joe MacEnri is a chartered engineer and ACCA qualified accountant who has worked in the electricity industry and asset management fields for over 35 years. He has many years of experience in the areas of techno-economic and investment analysis in areas such as capital plans and as well as reliability-based investment analysis using Monte Carlo simulations. He has worked with the multinational plastic manufacturer Sabic in their annual capital planning, training staff in the SALVO process and tools, facilitating workshops on individual investment studies, and working with sites to develop their annual constraints optimized capital plans using the AI powered DST Strategic AM Planning module as well as aggregated optimized multi-site regional plans.
With over 32 years of Asset Management, Reliability and, Mechanical Engineering experience in leadership, technical, and operational roles in Oil & Gas, and the Petrochemical industry. Pedro brings a proven track record of success in developing and implementing asset management processes and tools, to facilitate communication between engineers and managers, while establishing a direct connection between business objectives and frontline engineering and operational actions, with strong considerations of Fit for Purpose and Life Cycle cost factors.
Pedro is a strong advocate and Change Agent for cross-functional collaboration between departments orientated to achieve alignment of objectives for the development of efficient and effective asset management solutions. Pedro heads up our Australiasia business unit.
Victoria is a Principal Consultant & our Product Manager for the SALVO Decision-Making Framework.
She has over 20 years’ asset management experience, across transport, energy and defence sectors and is a specialist in asset management decision-making and risk management.
With plenty of hands-on experience developing optimized, risk-based asset maintenance and renewal strategies, and deploying these to develop multi-year investment plans, her industry positions include the Head of Asset Management (Electrical Utility), Manager Network Risk & Performance (Electrical Utility), Associated Director, Safety and Engineering Systems (Government Transport Agency), Team Leader, Asset & Risk Management Systems (Electrical Utility), Team Leader, Structural Safety, Risk & Reliability (Government Highways Agency)
Patrick is a specialist in data-enabled business transformation design and executive-level delivery governance to enable asset- and workforce-intensive organizations to deliver better customer and operational outcomes. He has 30 years of experience in the industry, working at the executive and board levels with critical national infrastructure organizations to shape and lead major value-realization programs with data and digital enablers at their core.
His core skills include Data strategy, Transformation design, Strategic roadmap development, Transformation governance and assurance, Transformation leadership, Business data services operating model design, Data skills and leadership development, and Leadership coaching, and mentoring.
Patrick is also a graduate of the Australian Institute of Company Directors (GAICD).
Susan Steyn is a seasoned expert with over 30 years of experience in Management, Operations, Business Development, and Supply Chain across diverse industries. Her core focus lies in spare parts management and inventory optimization. Throughout her career, Susan has held key leadership roles in multinational companies such as GE, Dow, Roche, Bayer, Lloyds Register, and Woodhouse Partnership.
With a strong background in strategic leadership, P&L management, and lean manufacturing, Susan has consistently driven business turnarounds and growth. She excels in international global business management and has a proven track record of expanding market presence and building strong client relationships.
As a Six Sigma Black Belt and PMP certified professional, Susan is adept at implementing process improvements and managing complex projects. Her expertise in data analysis, project management, and ERP systems ensures effective spare part management and optimal inventory levels.
Susan’s contributions to various companies include revenue growth, cost reduction, successful software launches, and the establishment of strategic alliances. Her commitment to diversity and inclusion, coupled with her leadership in team building and mentorship, have created a culture of excellence in every organization she has worked with.
Overall, Susan Steyn is a results-oriented leader with a passion for leveraging data-driven decision-making and innovative strategies to optimize spare parts management, reduce downtime risks, and enhance profitability in any business environment.
José Luis cuenta con una experiencia exitosa en multi-industrias públicas y privadas, donde desempeñó cargos gerenciales, líder de aplicación técnica especializada, puestos operativos y en mantenimiento, así como en áreas de consultoría sustentando nivel operativo, táctico y estratégico.
Ha formado parte de proyectos de mejoramiento de gestión de activos, confiabilidad operacional, integridad y mantenimiento en Latinoamérica en diferentes empresas creando valor al negocio con resultados técnicos y económicos importantes.
Facilitador e instructor acreditado en temas relacionados con la gestión de activos, mejores prácticas, metodologías de administración gerencial y técnicas especializadas.
Mechanical Engineer with 31 years of experience. Specialist in implementation processes of activities
associated with Asset Management under the ISO 55001 approach, Implementation of diagnostic
programs and audits of management systems, Specialist in applying reliability methodologies such as
Reliability-Centered Maintenance, risk-based inspection, Cause Analysis Root, Life Cycle Cost Analysis,
Condition Based Maintenance, Failure Modes and Effects Analysis, Mechanical Integrity among others.
He has been an Equipment Mechanical Integrity Engineer, an experienced user of traditional NonDestructive Testing such as Ultrasound, Infrared Thermography, Superficial Techniques, Industrial
Radiography.
He has led and participated in countless applications in the field of reliability and condition monitoring,
with special emphasis on the generation and execution of policies and maintenance plans aimed at
achieving the “minimum total business impact” guaranteeing Safety, Hygiene and Environment
standards.
Over his 28 plus year span in the industrial sectors with working technical backgrounds in Project & Construction Management, Asset Operations and Maintenance Reliability Management, and being certified in various courses of study; Damien has gained the knowledge and experience and has had proven successes throughout his tenure in the Oil, Gas, Petro-Chemical and Construction sectors. Establishing his-self in the various sectors, Damien’s first experience and success started in the Construction Sector in estimating engineering. This was the stepping stone for Damien and has paved the way for his passion and continued success in supporting People, Process, and Systems in an organization.
Damien has held positions in local, international and multi-national corporations and comes from a working background in the fields of environmental, operations, project and construction management, operations maintenance and reliability management, planning, supervisory management, and has proven his abilities to succeed in each field.
Rich was an Engineer and Project Manager professional at the New York Power Authority for over 30-years. In addition to being the first Project Manager for the Niagara Project Upgrade, Rich rose to be the Vice President of Engineering having started in Operations Engineering decades earlier. Rich went on to be Vice President, Transmission and Substation at AECOM responsible for hundreds of millions of dollars in design and construction. Rich joined Woodhouse Partnership, North America and participates in aligning organization towards ISO 55000 and many reliability studies supporting DST.
Executive in Operational Excellence, Asset Management and Best Practices in Projects, Operations and Maintenance in the Energy and Industrial Sector.
Consultant, Instructor and International Lecturer on issues related to project management (risk management), operational reliability, strategic management of operations, maintenance, Asset Management in the energy sector (ISO 55001) and Applied Data Analytics.
PMP, CMRP, IAM and CAMA certifications, being recognized by the SMRP in 2019 as CMRP of the Year https://smrp.org/2019-CMRP-Winners.
George has over twenty-five years of experience as a consulting engineer providing design, planning, program and project management, and strategic asset management services for asset-intensive organizations in the Americas, Africa, and the Middle East. His primary focus has been in the public infrastructure sector; as a result, he has intimate knowledge of the assets, processes, and resources necessary to deliver and sustain safe, reliable services to the customers of public asset-owning organizations.
George has assisted organizations with the development of PAS 55, ISO 55000, and GFMAM AM Landscape aligned asset management systems (AMS), has performed gap analyses of their AMS against industry standards and best practices, and has guided them through the creation of strategic asset management plans (SAMPs), asset management plans (AMPs), AM policy and supporting documents. He has undertaken asset risk modelling to ascertain organizations’ capability to sustain their desired levels of service. George has performed asset health-informed lifecycle cost modelling and forecasting capital and operational expenditures over near and long-term planning horizons.
With 30 years’ experience in utilities, oil & gas, transport and other sectors, John is one of the most widely known experts in integrated asset management projects for some of the largest companies in the world.
John is a Founder and Life Fellow of the IAM; he has written 4 books, chaired the development of BSI PAS55 and represents the UK on the ISO55000 committee.
He also led the international MACRO and SALVO collaboration projects in optimised asset management decision-making.